Hand Washing without Human Error – Redesigning the Tap
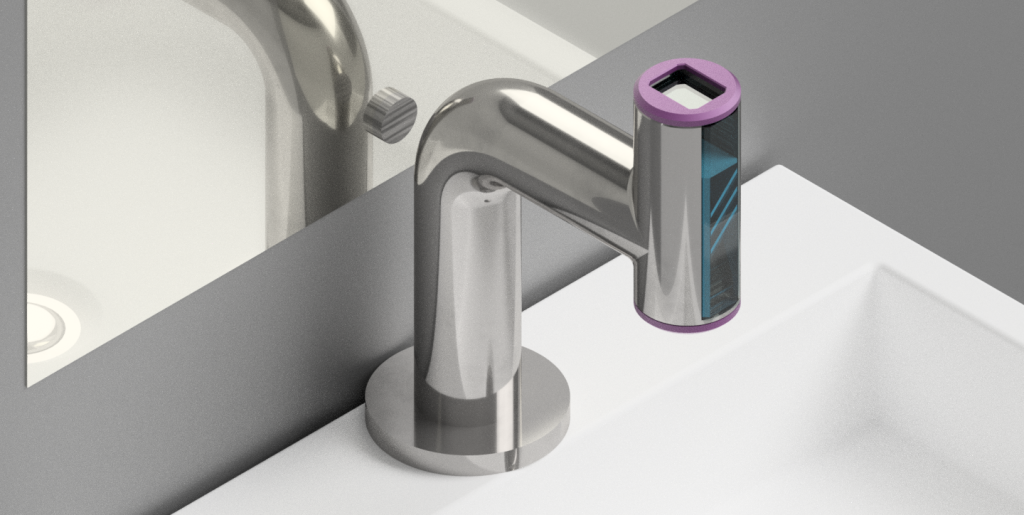
Client:
University Project
Date:
Sept 2021 – May 2022
Overview:
The problem that I chose to tackle in this project was poor handwashing adherence; only 5% of people are washing their hand correctly after using public restrooms. Through the course of the project I developed an novel type of automated hand washing device, a soap foam jet integrated into a tap. The user would scrub their hands underneath the flowing stream of soap foam for a set amount of time before the tap would switch to just water allowing the user to rinse off the foam. This simplifies the hand washing process and prevents common user errors seen with traditional hand washing and other automated handwashing systems. You can’t wash with water alone, you can’t wash the soap off too early, and you are encouraged to wash for the correct length of time while also making the process simpler and more enjoyable for the user. The product can be retrofitted into any existing bathroom and will be comparable in price to existing auto taps while delivering much better cleaning results. I took this project all the way from a single sentence problem statement, to a refined working prototype and separate appearance model, both that were tested in the real-world with users.
Problem & Aims
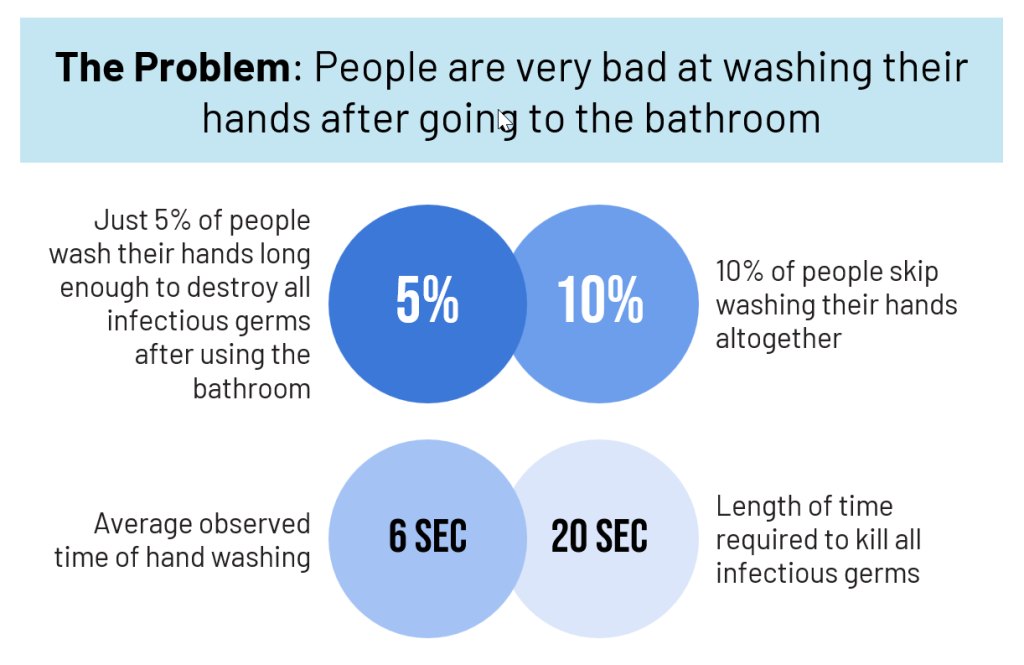
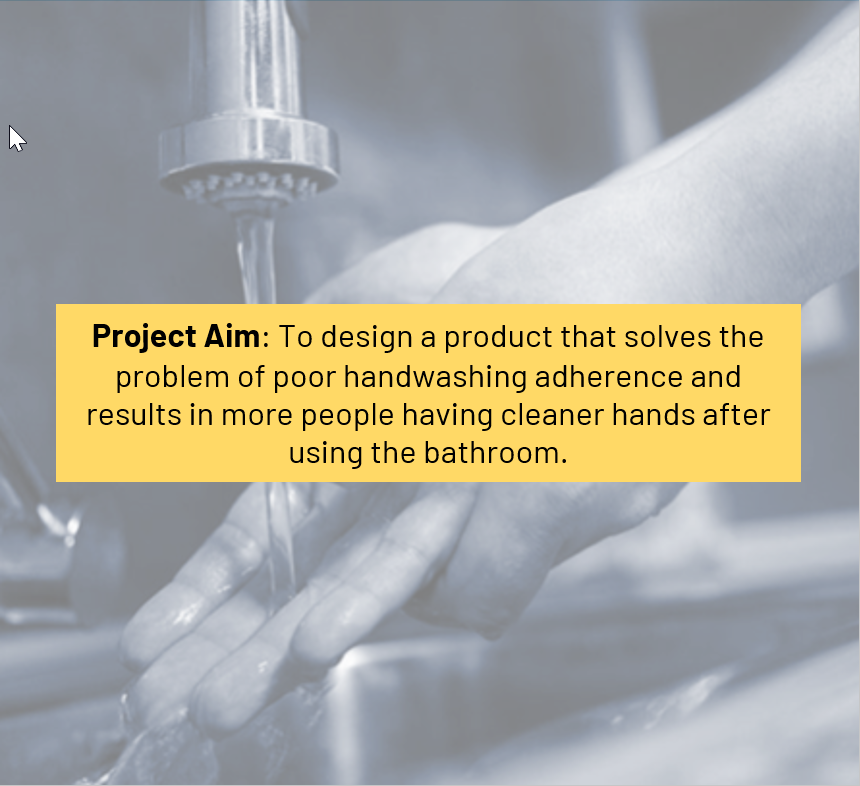
Early exploratory work
Before jumping straight into designing a new product, it was important to explore the problem. The main activities carried out were a market analysis, developing a test method for measuring hand cleanliness, and carrying out exploratory testing.
Market Analysis
In the market analysis, several product categories were identified and analyzed. Ultimately the initial project strategy was to create a simplified, cheaper version of the industrial Meritech product that appeals to the public and commercial bathroom market (the Meritech being a fully automated handwashing machine used industrial clean room settings). The new product would achieve the gains in cleanliness through automation, removing the user error from the process. While the lower price would make it competitive with other products currently in the public and commercial bathroom space, making it more popular, which gets more people using it. The diagram shown below illustrates how the new product would compare to existing products.
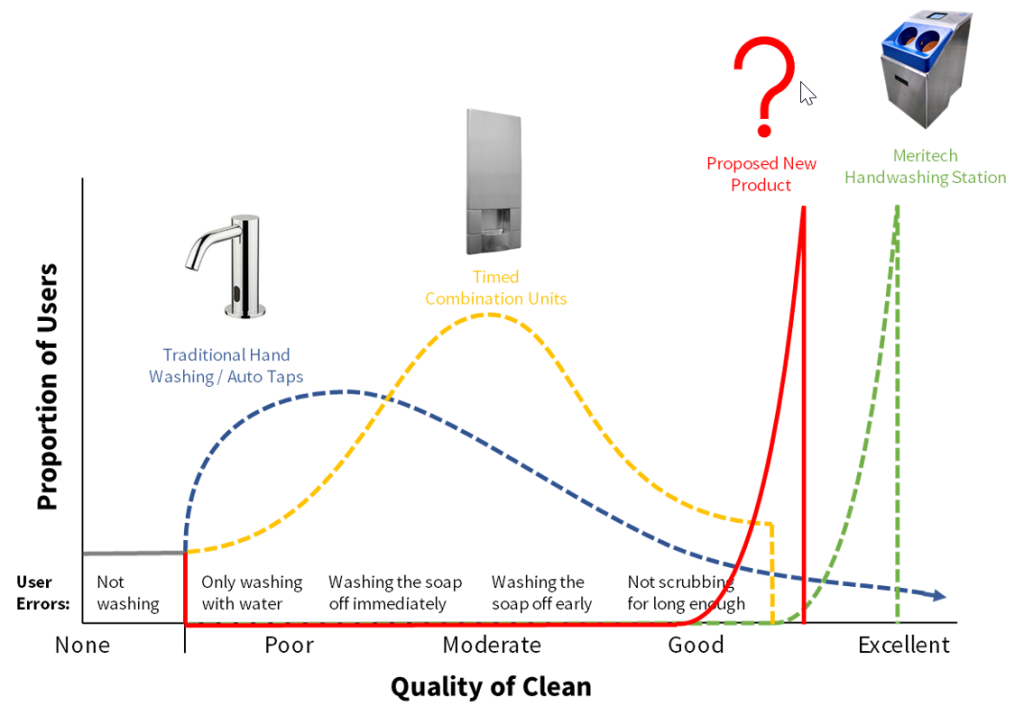
Using the results of the market analysis and this initial design direction, three critical success criteria were identified.
Hand Cleanliness – This refers to the average cleanliness of users’ hands after using the product under real world conditions. It cannot be assumed that users will use a hand washing system/product as intended if there is room for human error. As previously mentioned, when observed under real world conditions, only 5% of people are following the correct hand washing procedure when using a traditional hand washing system. Therefore, in the context of product comparison, hand cleanliness refers to both how good a system is cleaning hands when used correctly and how likely it is that users will use the system correctly.
User experience – This refers to how much users enjoy using the product. Multiple elements of the design will contribute towards the user experience such as its aesthetics, its intuitiveness, the sensations of the cleaning process, convenience of use, and more. The is an important factor for two reasons. Firstly, if the product is enjoyable to use then hand washing becomes more enjoyable, and users will be less inclined to skip washing hands altogether which improves hand cleanliness. Secondly, it makes the product more desirable to potential customers.
Customer Appeal – This refers to how appealing the product would be to potential customers, the customers being architects and facility mangers. Besides Hand Cleanliness and User Experience, there are a number of other factors that customers consider when choosing a new hand washing system. Some of the most important factors that they consider are:
Developing a hand cleanliness test
Early on in the project, I realized that it would be very important to develop some sort of repeatable test procedure that would allow me to measure hand cleanliness. Especially since I identified hand cleanliness as one of the three critical success criteria. The test method that I developed consisted of applying a UV disclosing gel to a user’s hands before washing, carrying out a hand wash test, and then taking a photo of the user’s hands under UV light. Any gel that is left on the hands will glow under the UV light. The photos can then be compared to judge the relative performance of different hand washing techniques and mechanisms.
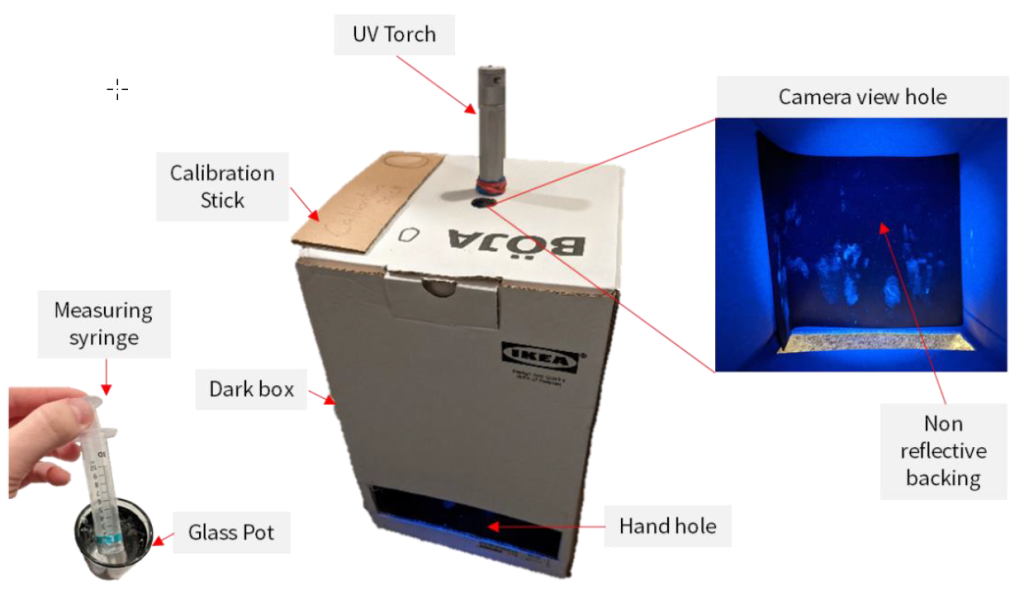
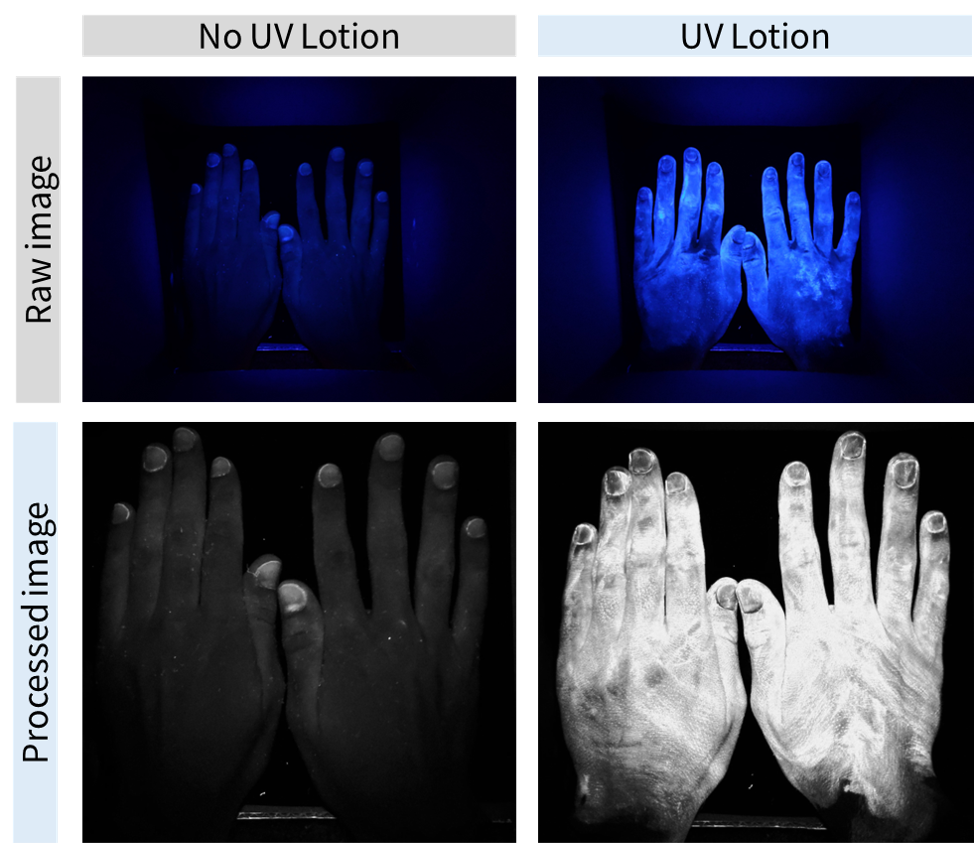
Using this hand cleanliness test method, several experiments were run that investigated the effectiveness of different hand washing techniques and mechanisms. The key findings from these experiments were:
- Hand soap plays a big role in the hand washing process. Without it, it was impossible to get a good clean.
- In all tests, a film of hand soap was first applied to the hands before cleaning. All the aggressive water-based mechanisms that were tested (rinse, spray, agitated vortex soak) gave worse results than doing nothing and leaving the film of hand soap untouched for the duration of the test. I hypothesized that the aggressive water-based mechanisms were washing away the film of soap, hindering the cleaning ability of the mechanism.
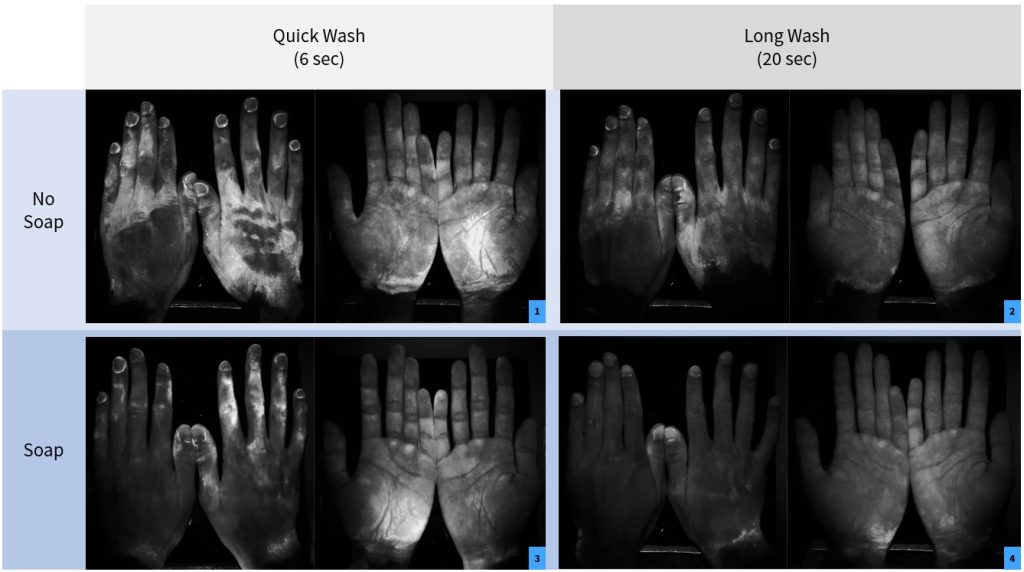
Based on the findings from these experiments, several key project decisions were made:
- The cleaning mechanism must incorporate use some form of soap or detergent to aid the cleaning process.
- The cleaning mechanism must wet the hands before or during the application of soap/detergent to allow it to function properly.
- There must be a rinsing stage towards the end of the cleaning process to remove any remaining soap/detergent from the hands.
- If a form of water jetting is used (Mist, rinse, spray, jet), soap/detergent must be continuously incorporated into the stream so that it can’t be washed off.
Concept Generation and Development
Alongside the market analysis and test procedure development, I was also carrying out concept generation. I started off by running several group ideation brainstorming session, bringing in classmates to contribute.
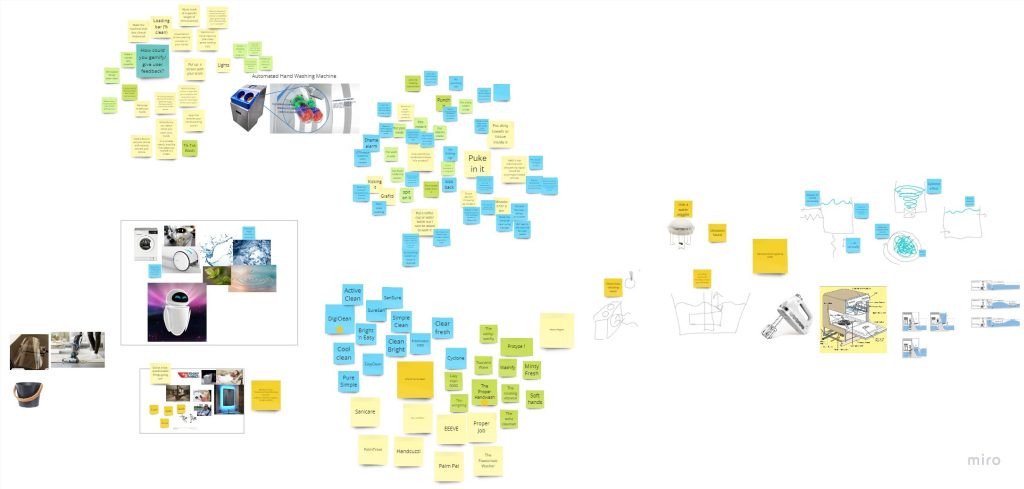
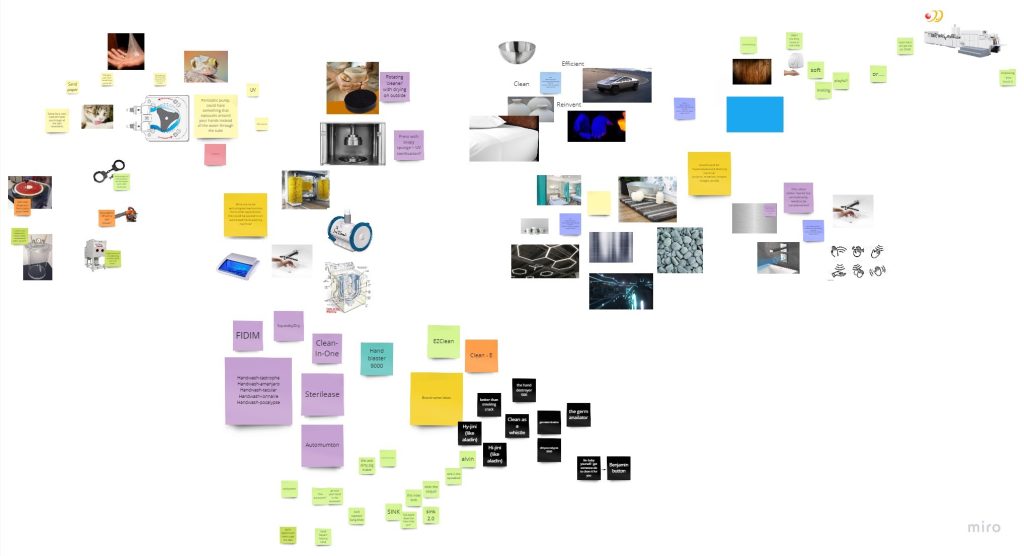
Based on the brainstorming and further research I was able to do some feature/technology grouping and summarized the brainstorming results in table form.
Cleaning mechanism idea groupings:
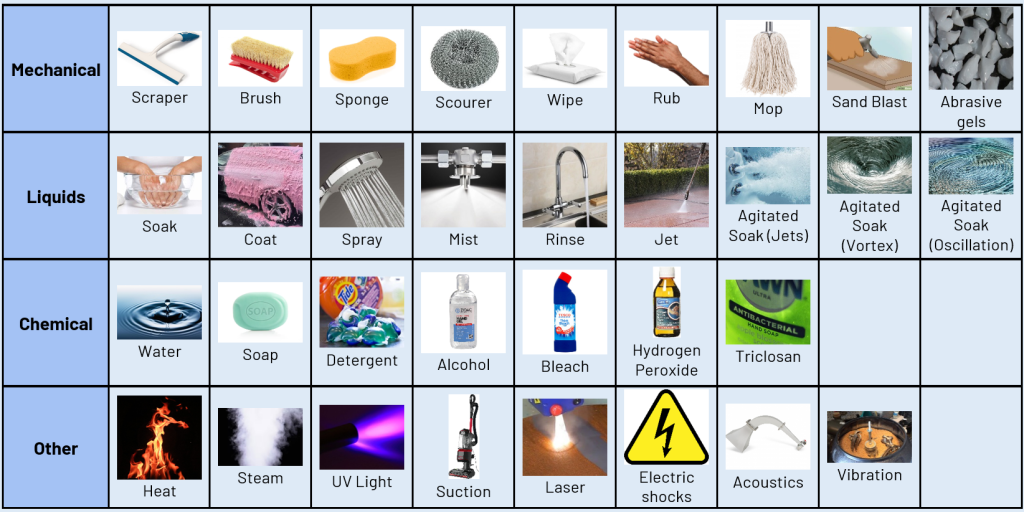
Additional feature ideas groupings:
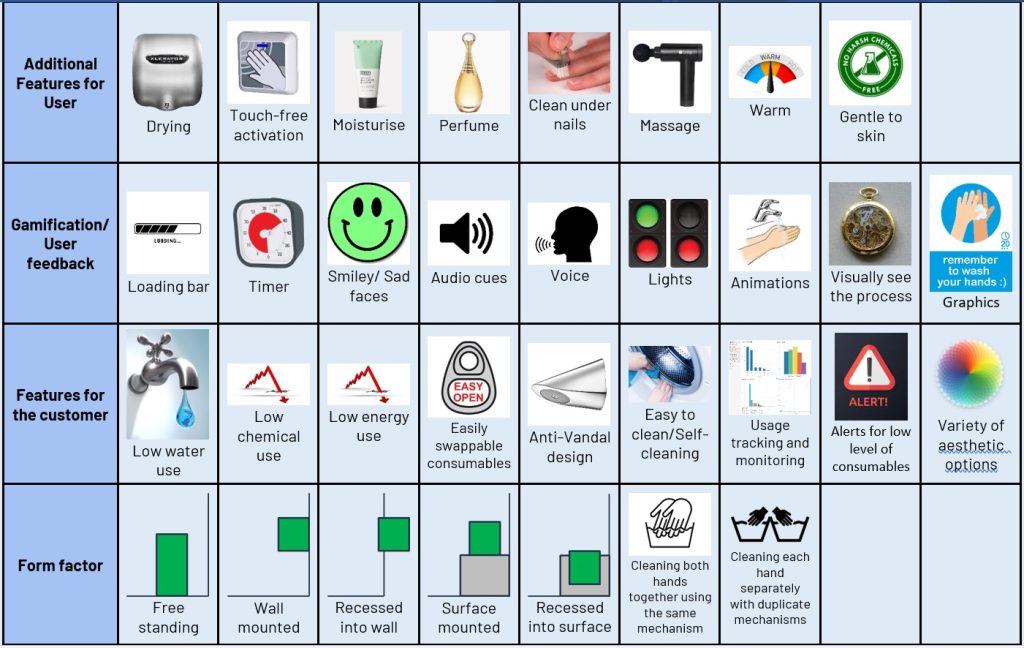
From the concept generation session, three concepts were created using a combination of the feature groupings. These concepts are shown below. Based on the test results from the cleanliness testing and evaluating the concepts against the 3 critical success factors, foam jets concept was chosen for further development. It consists of a machine that the user places their hands into and holds them still while they are sprayed by an array of soap foam jets. These jets introduce a cleaning solution into the water stream and continuously produce a foamy soap spray.
Concept 1 – Foam Jets (chosen concept)
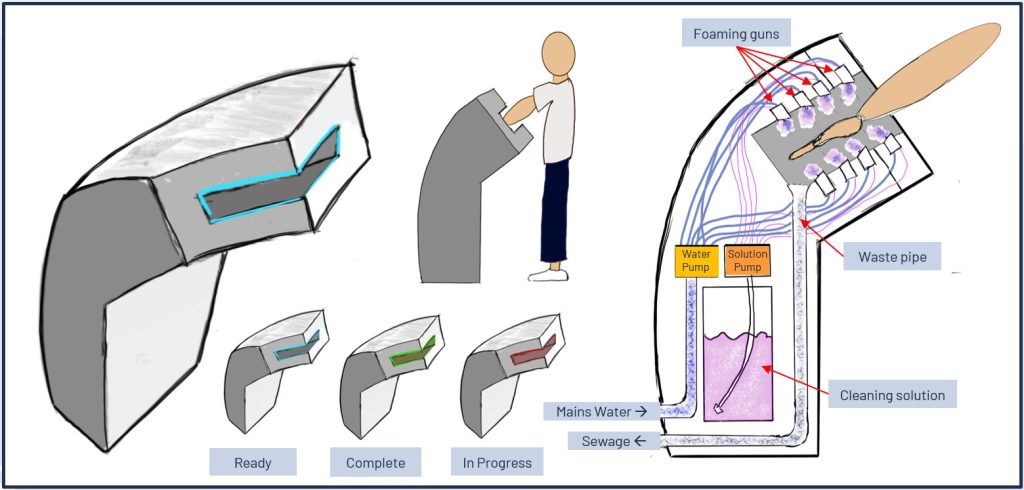
Concept 2 – Agitated soak (not chosen)
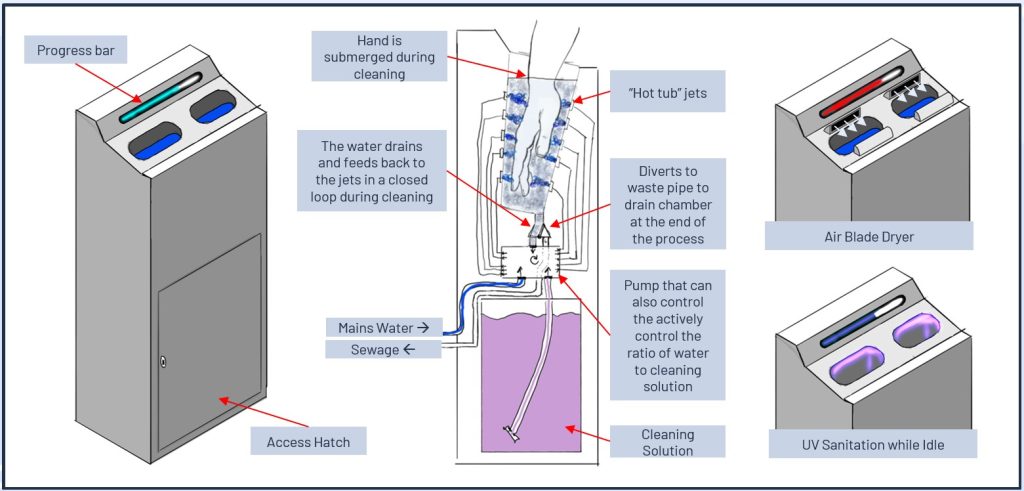
Concept 3 – Brush roller (not chosen)
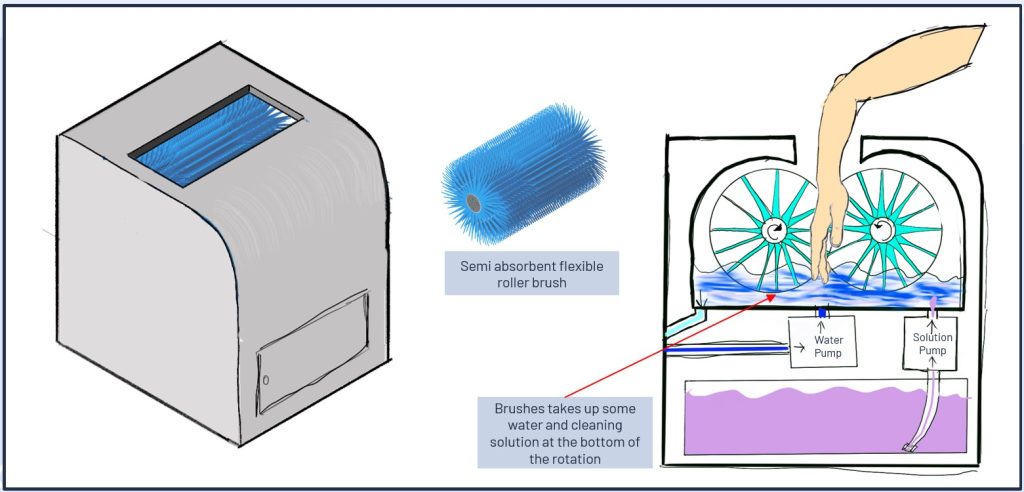
Development Sprint 1
With the initial design direction set, the next stage was developing and de-risking the concept. This would make up Development Sprint 1 (DS1). The main risks with this concept were:
- How would these soap foam jets work?
- Could this array of soap foam jets give good enough cleanliness performance?
It was decided that the best way to address these risks would be to build a working test prototype. The prototype would be a simplified version of the cleaning chamber part of the concept. Through the process of building it, an understanding of the soap foam jet mechanism would be gained, and the completed prototype could be tested using the UV Gel method to determine its cleanliness performance. The approach taken for the building of the test prototype was to quickly iterate using existing products and components. Due to the difficulty of prototyping systems that must withstand pressurized water, the test prototype was built largely from modified garden hose accessories.
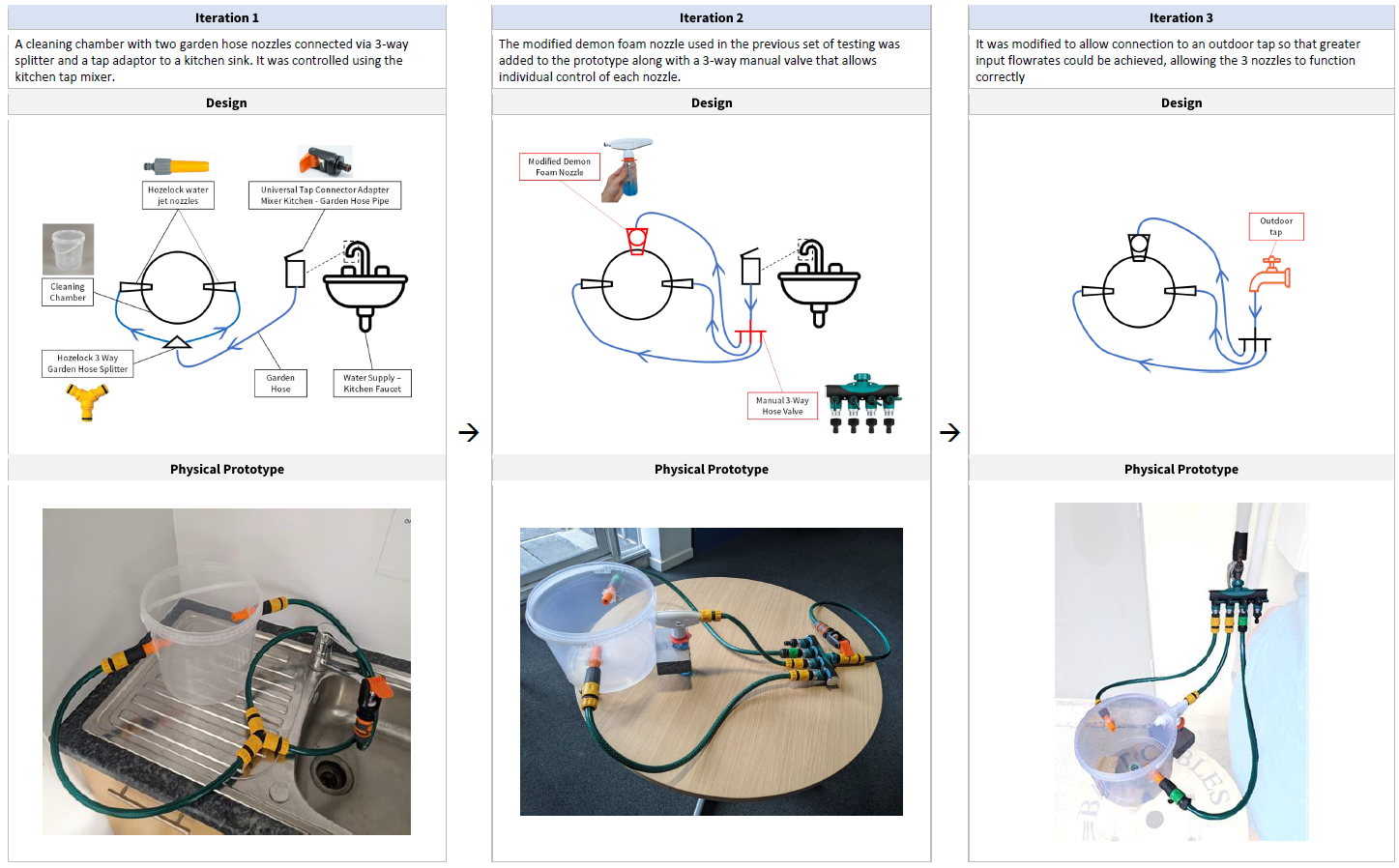
By the third iteration of the test prototype, it was ready for testing. The next stage was carrying out UV testing to determine the effectiveness of the soapy jet, water jets and hand scrubbing on hand cleanliness. The key findings from this set of testing were:
- The water jets don’t improve the quality of the clean by a significant amount. They are useful for rinsing the foam off the hands at the end of the clean, however there is no need for multiple high powered spray nozzles. The same rinsing function could be achieved with a single low flow rate water nozzle.
- The manual scrubbing of the hands does improve the quality of the clean by a significant amount.
- A very good clean that is significantly better than traditional hand washing (based on the average user behaviour of a 6 second wash) can be achieved with the soapy foam nozzle alone if it is combined with manual hand scrubbing.
Based on these findings, it was decided to halt development of the test prototype since all the original questions that this prototype was built to investigate had been answered. The results of this testing threw into question many aspects of the original foamy jet machine concept:
- Is there really a need for a whole array of soap foam nozzles if just one nozzle gives very good cleaning?
- Is there a need for high pressure jets at all considering that the increased pressure doesn’t have a significant effect on cleaning but introduces big problems with splashback?
- If the user still needs to manually scrub their hands, is this really a fully automated machine anymore?
- If we only need one low pressure soap foam nozzle, and the user needs to manually scrub their hands, why does their needed to be a cleaning chamber, could the design be more open?
These questions lead to a big shift in the direction of the project, and a change in design strategy.
Project Pivot
Based on insights and results gathered from the testing of the Test prototype, an alternative direction for the project became clear, both in terms of the design and the project strategy. An alternative concept to the original foamy jet machine was developed called “Smart Foaming Tap”. Since very good cleaning performance could be achieved using just a single foamy jet with manual hand scrubbing, why have multiple foamy jets and high-pressure water jets and all the added complexity and cost they would add? In this new concept, the design is based around a new hand washing process and a single nozzle that can spray both a thick soapy foam and water, which are integrated into a tap.
New Concept – Smart Foaming Tap
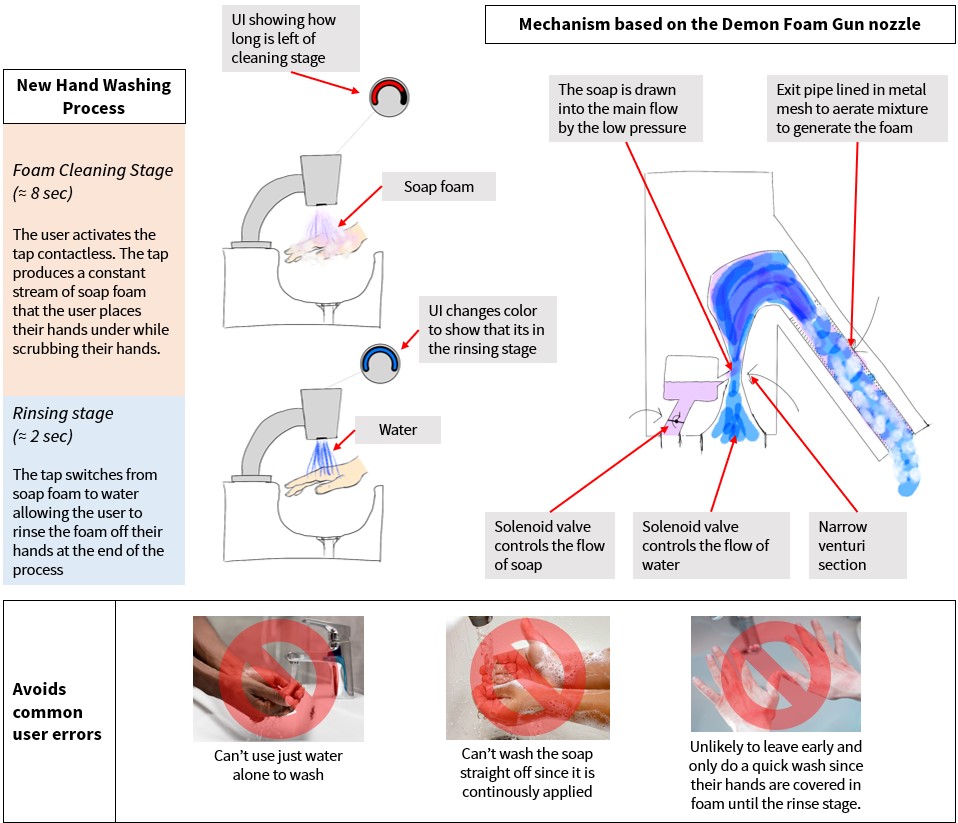
Change in market strategy
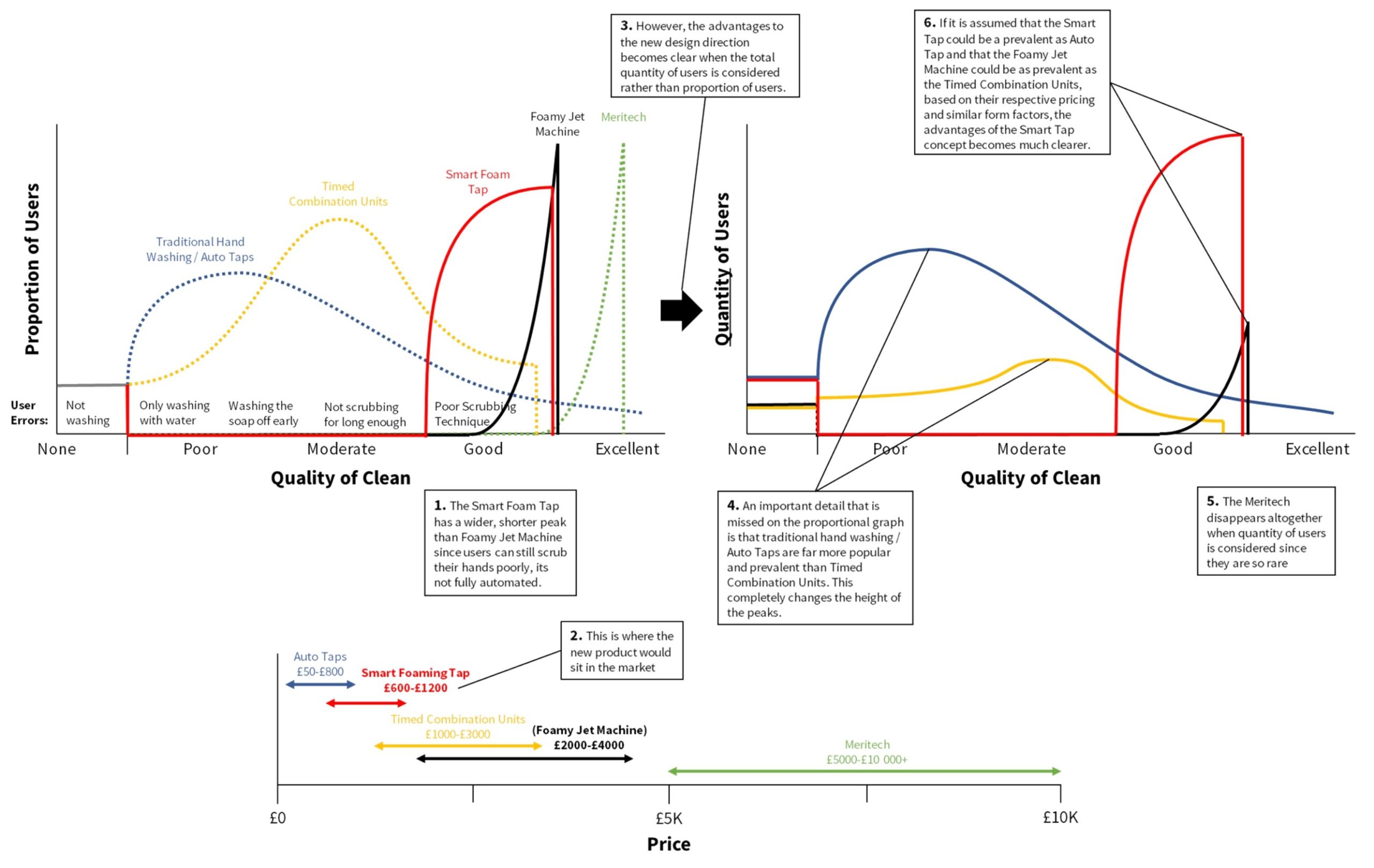
Development Sprint 2
With the new design direction and strategy set, the next stage of the project was to develop and de-risk the “Smart Foaming Tap” concept. In Development Sprint 1, the cleanliness performance of the test prototype was shown to be very good, and since the cleaning mechanism is largely the same in the smart foaming tap, this aspect of the design was already proven out. The focus of Development Sprint 2 was to prove out the User Experience and Customer Appeal elements of the design. The main questions that this development sprint aimed to answer were:
- Will users prefer using the smart foaming tap over traditional hand washing?
- Will users understand how to use the new system?
- Is there a significant benefit to the new product over other existing products that it appeals to customers?
To answer these questions, Development Sprint 2 had two main objectives that were worked on in parallel.
- To develop an appearance model that can used to gather feedback from users and customers. The appearance model will be used to refine the form, materials, intuitiveness, system architecture, etc.
- To develop a working principles prototype that can tested with users. The prototype needs to be able to carry out a full cleaning cycle (contactless activation, foam cleaning cycle, rinsing cycle).
Appearance Model Development
The first step in creating the appearance model was better defining the desired aesthetics, this was done by creating mood boards. The first mood board shown below was used to explore the elements of design that portray the themes of hygiene and cleanliness. Some common elements found in the selected images/products:
- Smooth, rounded edges
- Large, continuous, smooth surfaces and faces
- White and silver/grey being the primary colours
- A single bright colour used in contrast to the whites and silvers as an accent colour
- Stainless steel and white ceramics/hard plastics being the most commonly used materials
The seconds mood board, also shown below, was used to explore the designs of existing smart taps. Some commonly found design elements are:
- The use of LEDs and digital displays to convey the “smart” part of smart tap
- Lots of stainless steel/chrome
- Sometimes glass used as an accent material
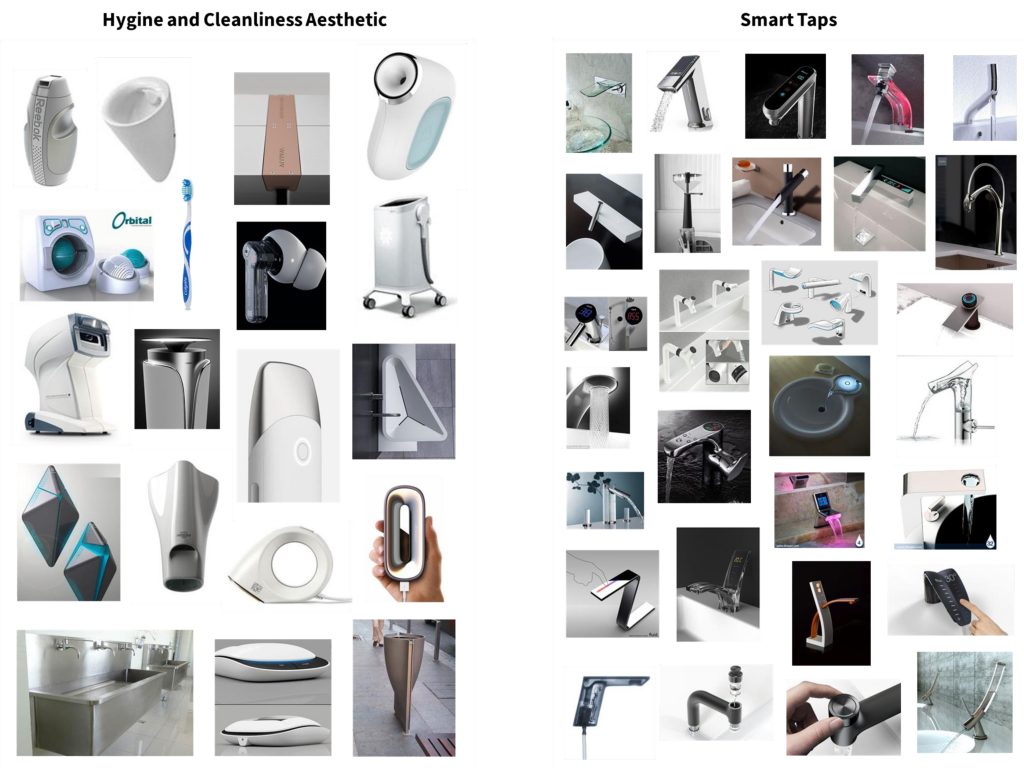
Based on the aesthetic features identified from the mood boards, I developed some sketches of what the new design could look like.
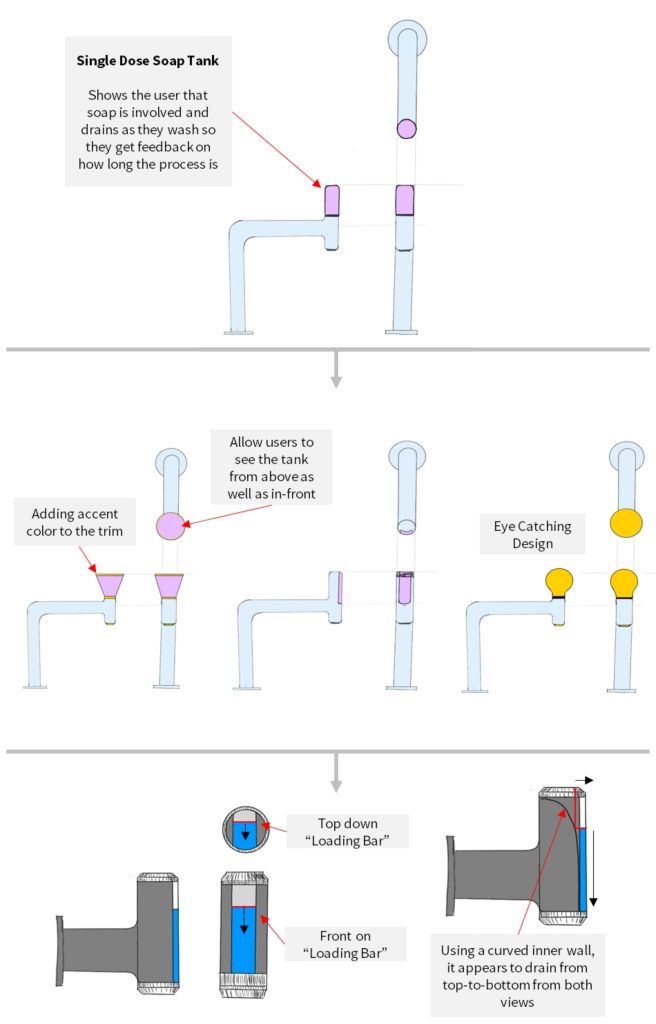
Based on the early sketches, expert feedback and mood boards, a complete appearance model of the product was developed in CAD.
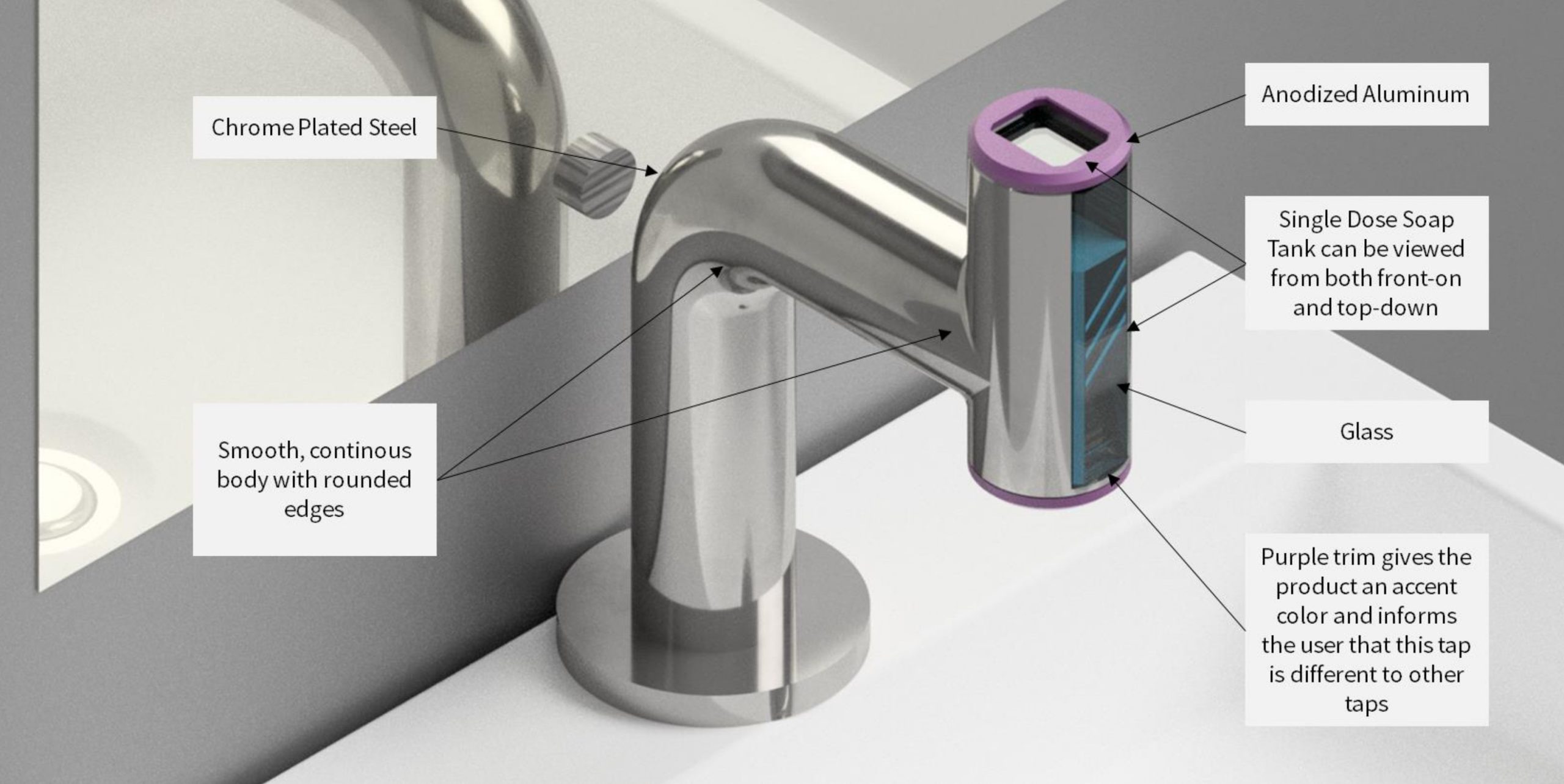
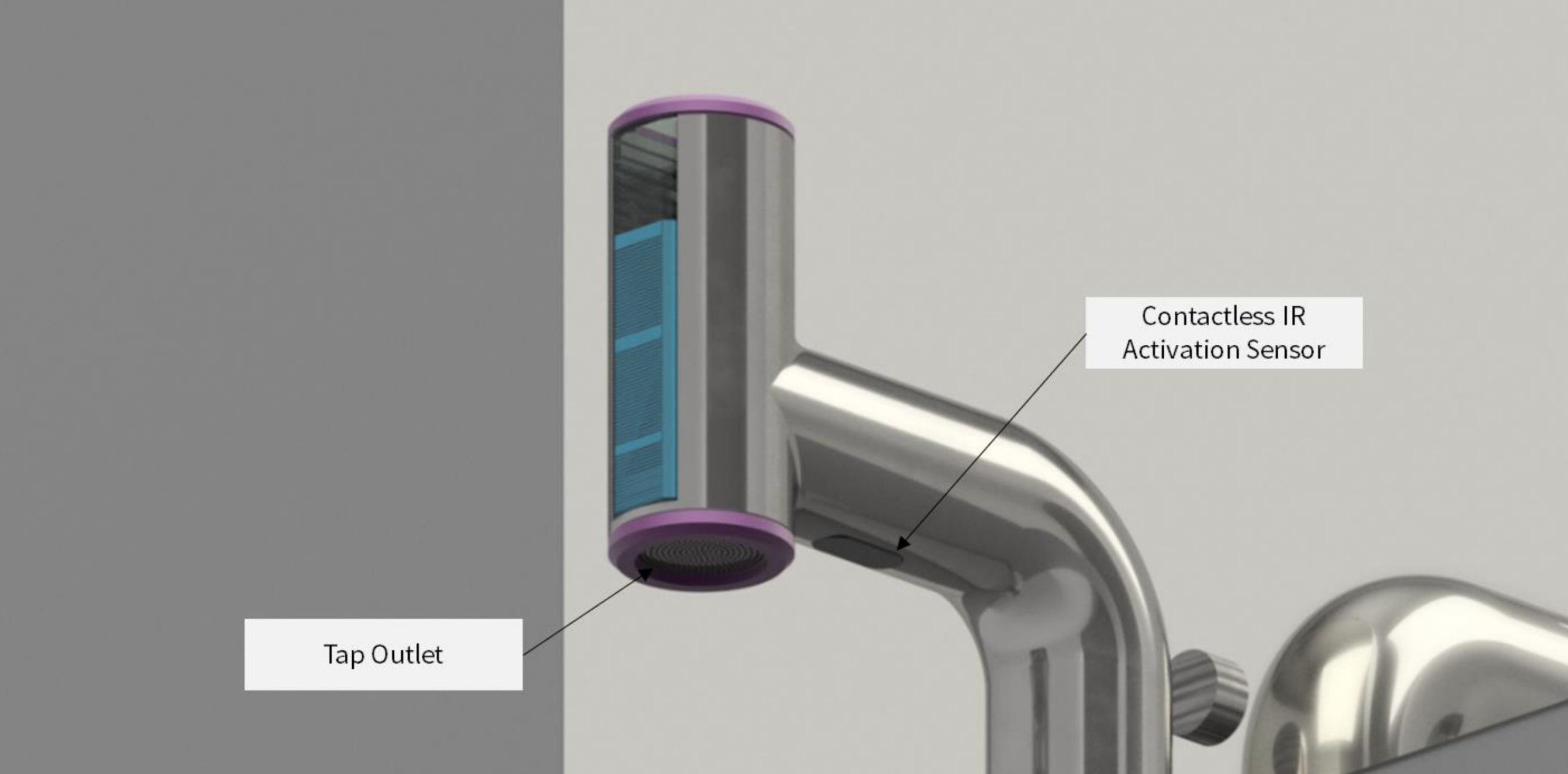
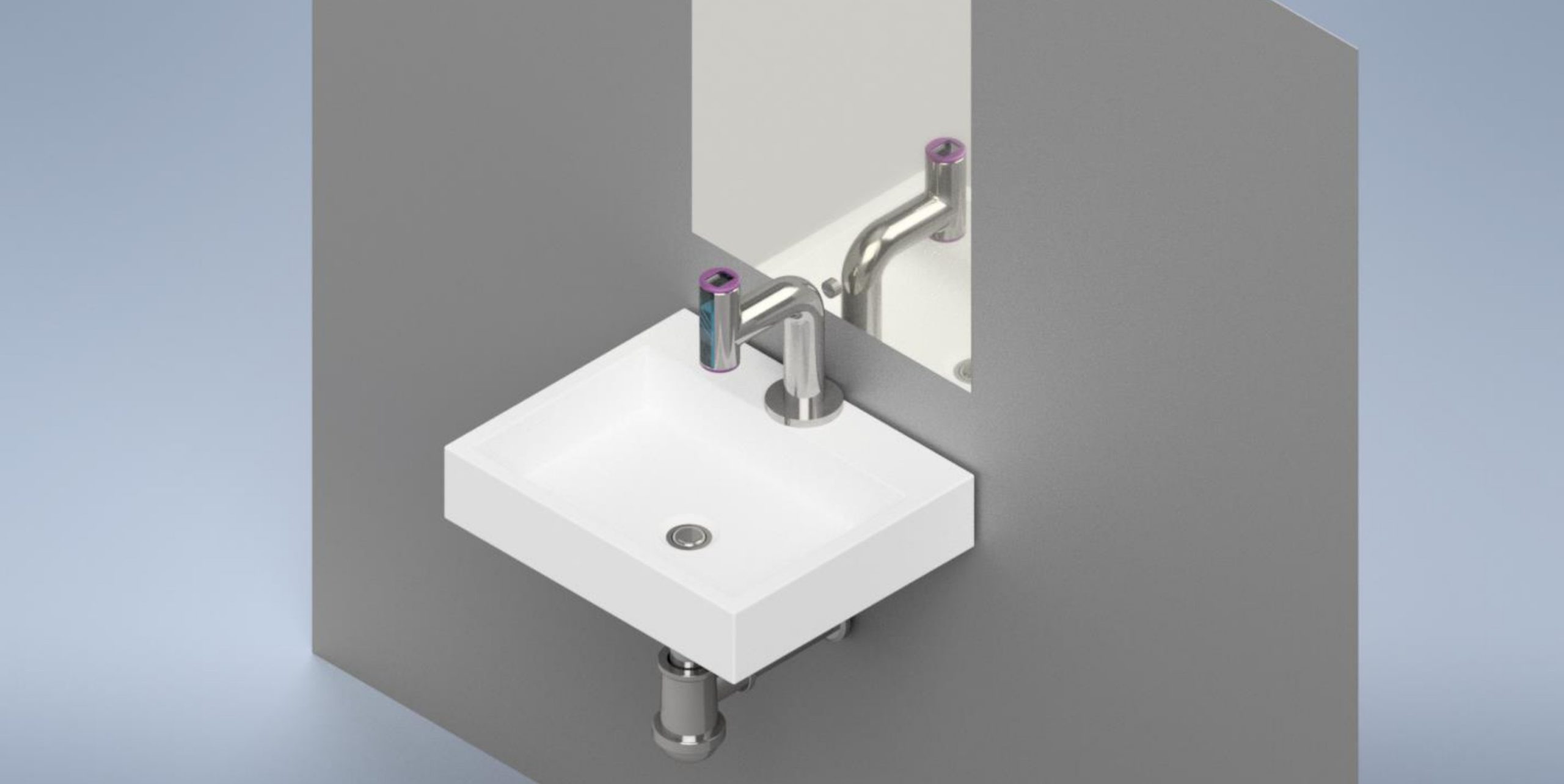
To gain understand as to whether the design improved the user experience and appealed to customers, it was presented to several potential users (lecturers and classmates) and to an expert in hand hygiene who could be considered an expert user and a potential customer.
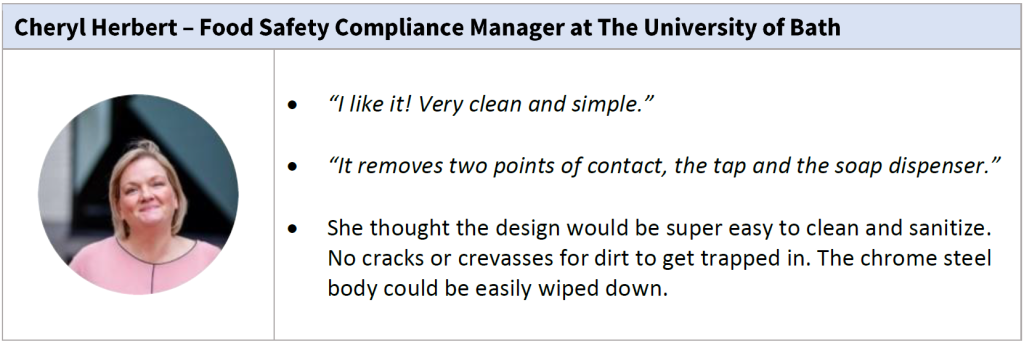
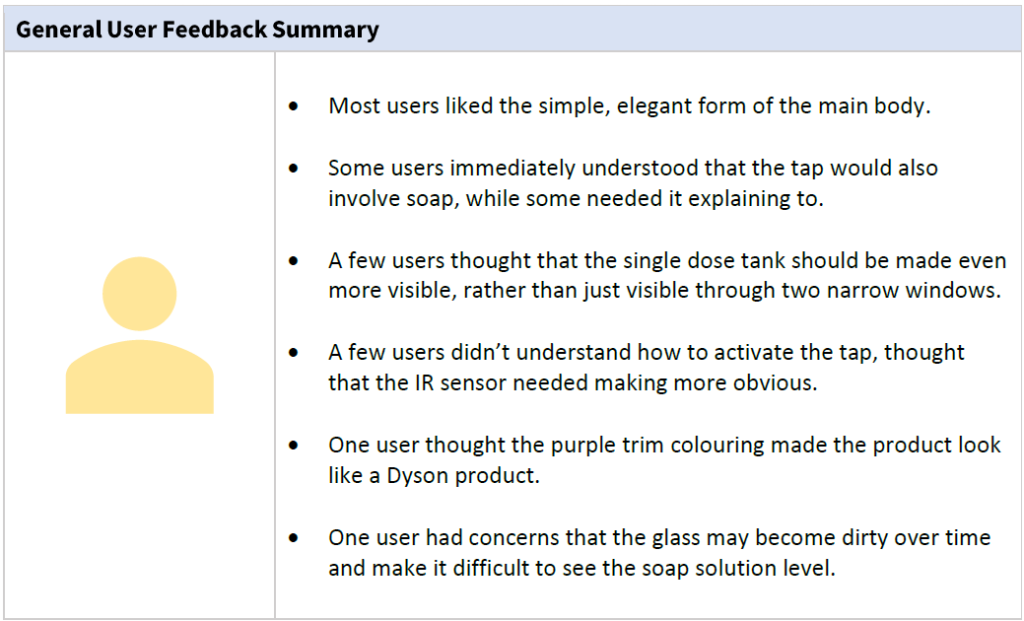
Based on the user feedback and an evaluation against Donald Normans’ design principles, it would be justified to state that the Smart Foaming Tap would offer some improvements both to the customer appeal and user experience of hand washing. To further de-risk the user experience and customer appeal of the product, the next stage was developing the working-principles prototype.
Working Principles Prototype
The second key deliverable from DS2 was the working principles prototype. The aim for this prototype was for it to be able to perform a complete cleaning cycle and to be tested with users.
Here is a system diagram of the subsystems involved in the physical prototype.
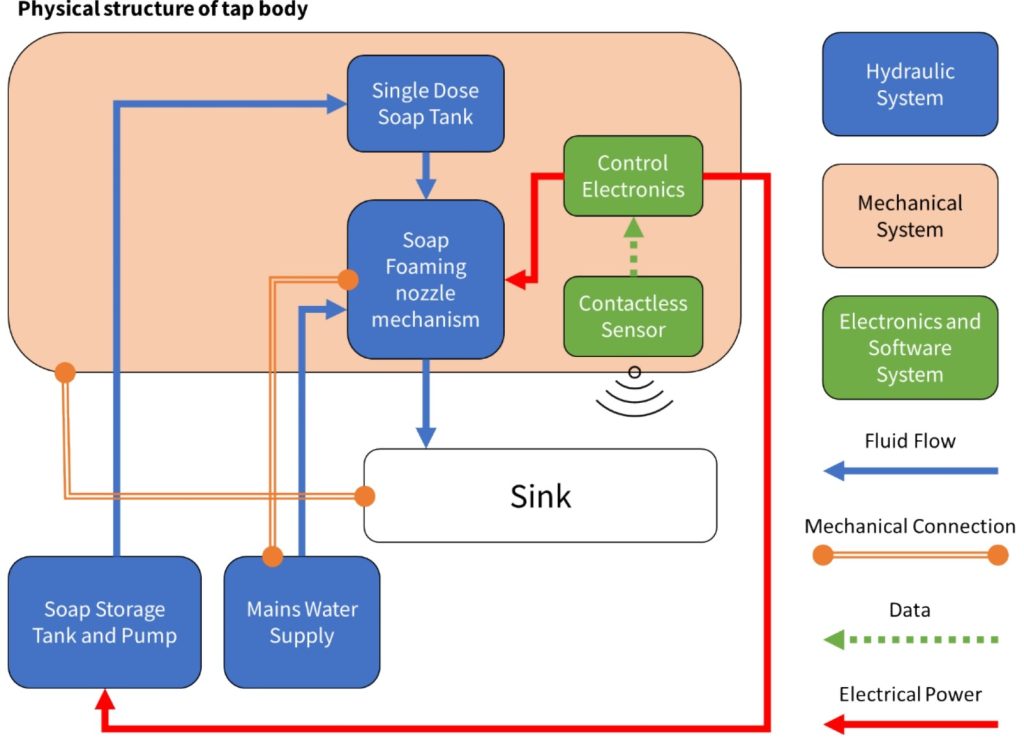
Development of the hydraulic system
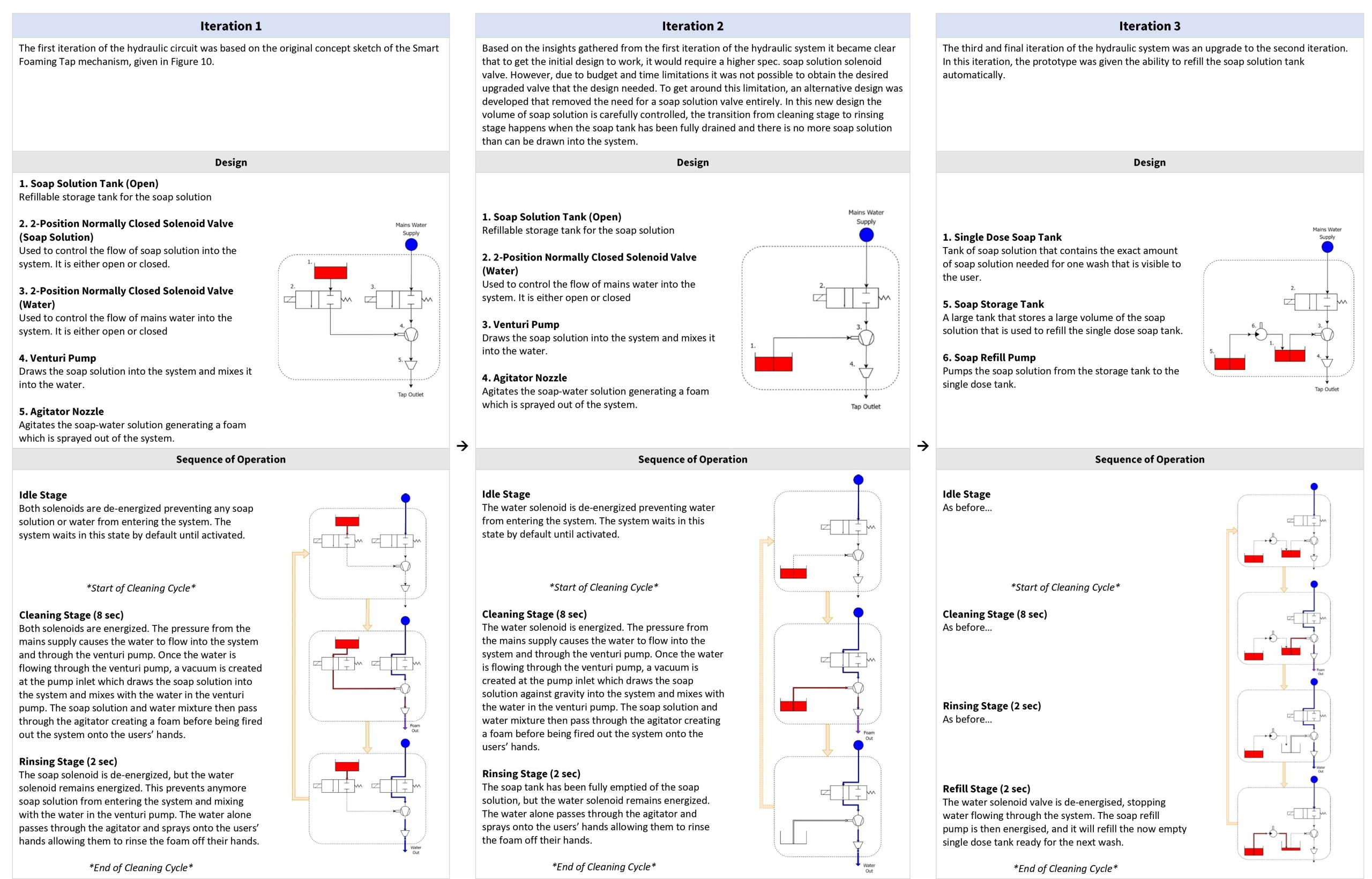
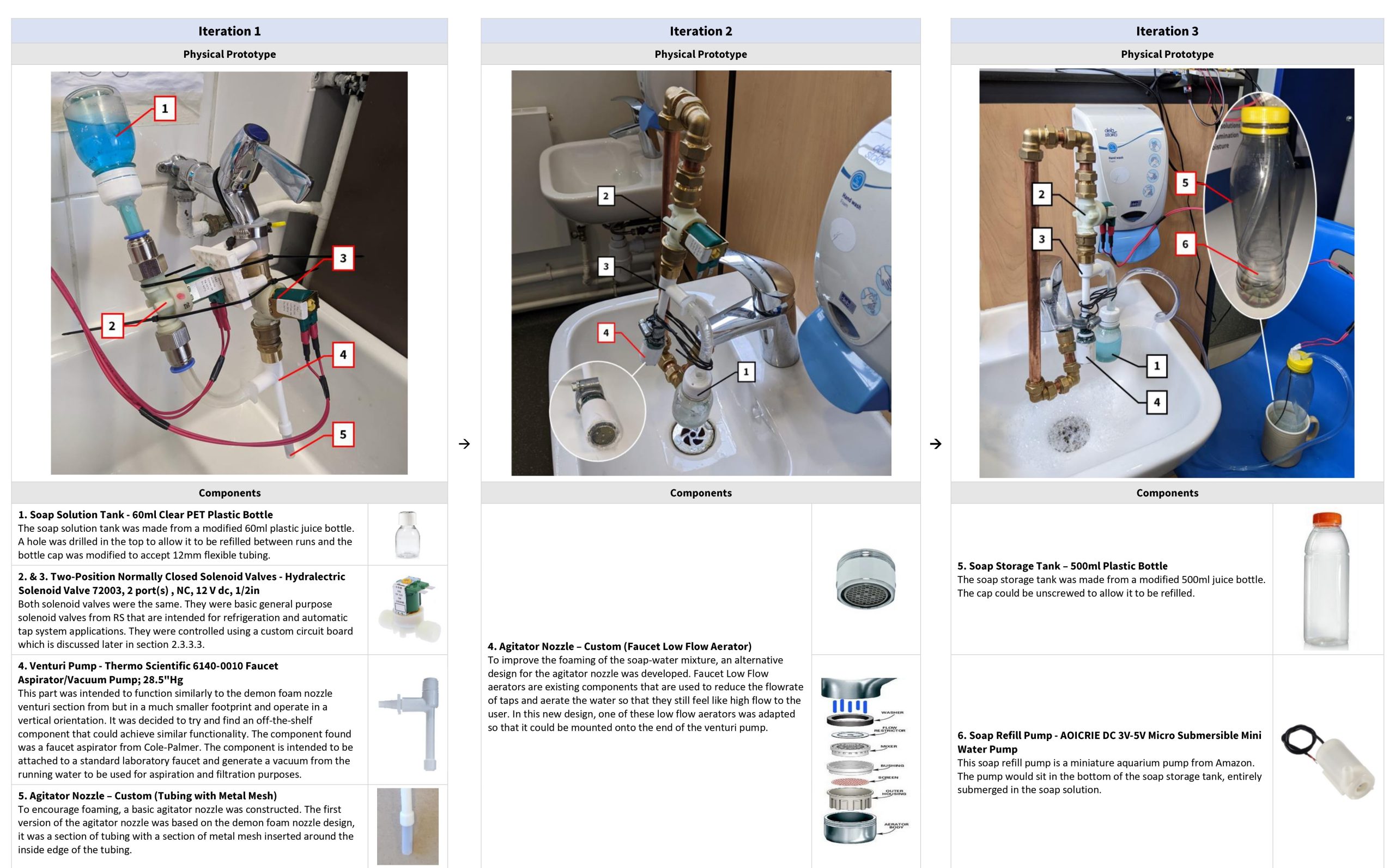
Development of the mechanical system
The mechanical design of the prototype was relatively simple. Early on it was decided that the prototype design should minimize the number of custom components due to the difficulty in prototyping custom parts that can withstand pressurized water. Therefore, the design was largely based around bought-in components.
The main challenge of the mechanical design was connecting each of the hydraulic components together in a reliable way. Each of the major components had either external threads or barbs intended for connection purposes. Therefore, the mechanical design consisted mostly of threaded brass adaptors, push fittings and flexible tubing.
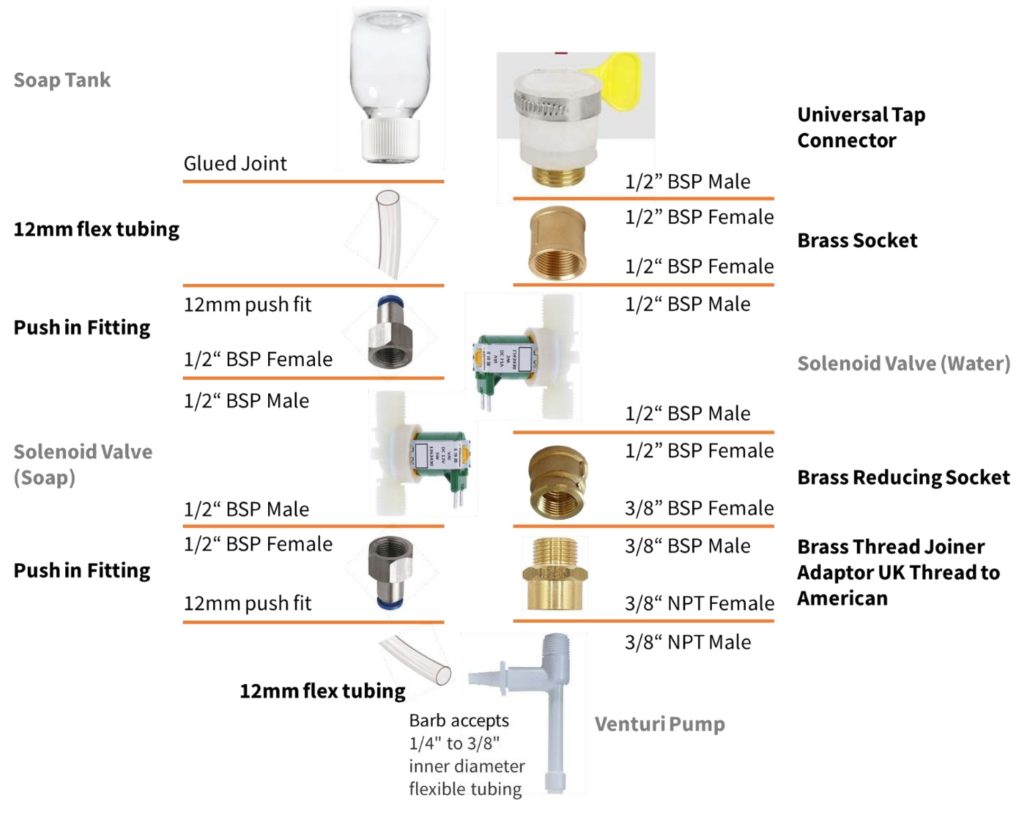
Developing the electrical and software system
The final version of the prototype was powered and controlled using a custom circuit board that I developed with the logic required to handle the working processes carried out on an Arduino nano. The electronic and software system went through several iterations to reach the final form shown below.
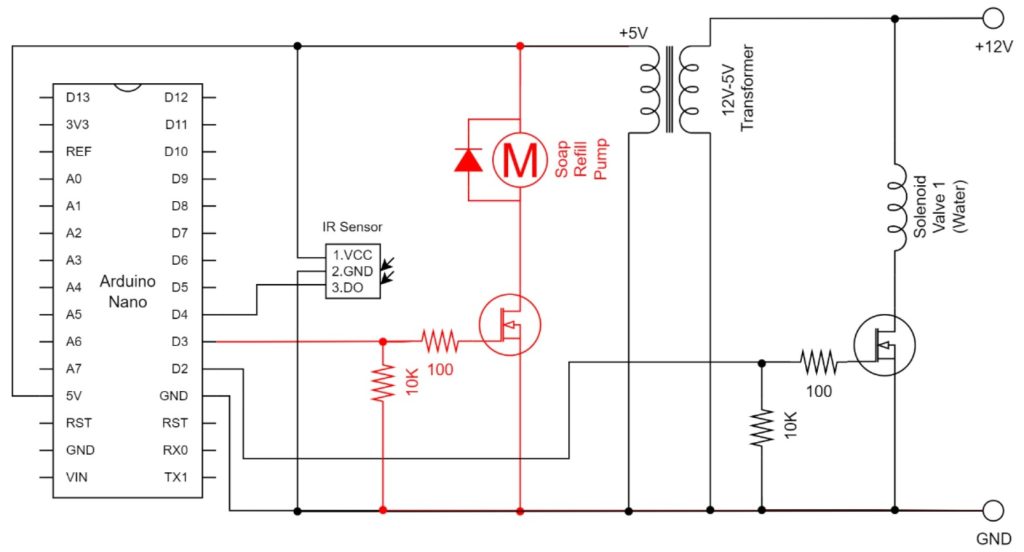

Testing the prototype
With a fully functional working principles prototype, the next stage was testing it. The testing of prototype was split into two types, cleanliness testing and user testing. The cleanliness testing consisted of using the UV gel test method to compare how well the prototype cleans compared to traditional hand washing. The user testing consisted of getting multiple users to try the product and getting their qualitative feedback.
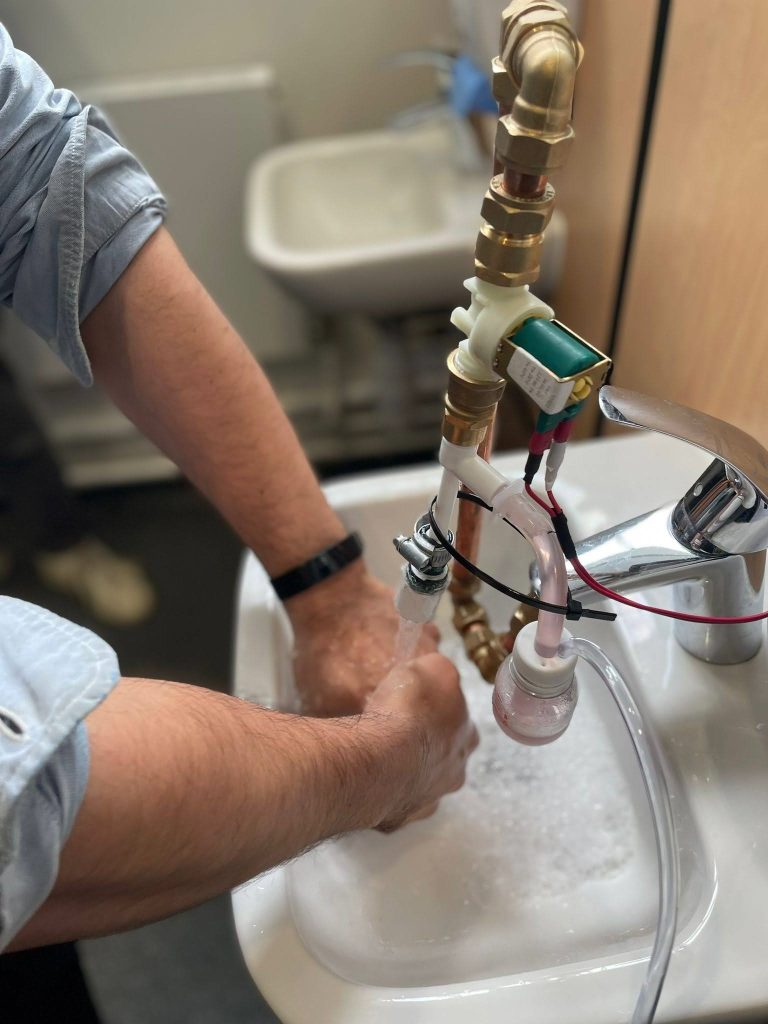
This is what one of the expert users had to say after using the product.
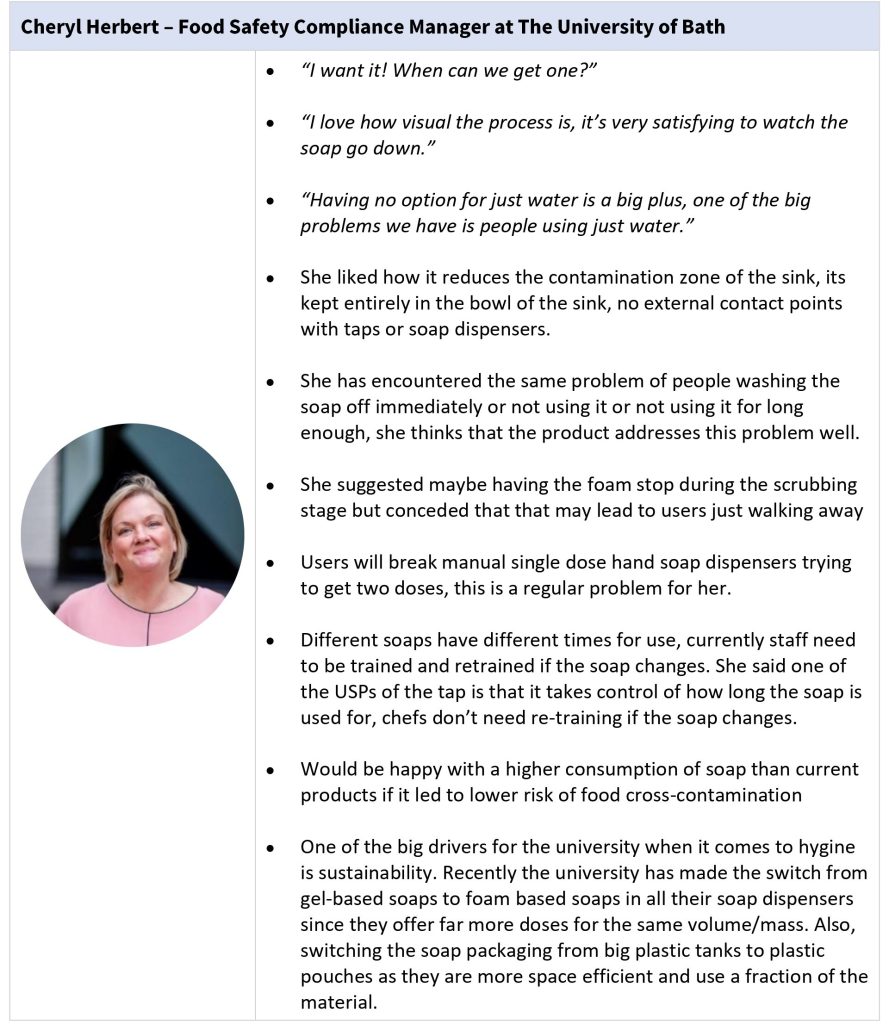
Project Conclusions
Overall, the aims for Development Sprint 2 were met. Through the development, evaluation and user testing of the appearance model and working principle prototype, it was proven that the Smart Foaming Tap product does offer a significant improvement to the user experience and customer appeal over existing products. The overarching aim of the project was to design a product that solves the problem of poor handwashing adherence and results in more people having cleaner hands after using the bathroom. The results from DS2 that suggest that the Smart Foaming Tap will meet this goal.
The current appearance model design portrays the desired aesthetics of cleanliness and hygiene through its use of smooth continuous surfaces with rounded edges, the use of chrome steel and glass. It also takes the best elements of other smart tap designs such as colour accents and showing processes visually but avoids the cluttered digital UIs and LEDs. The design was well received by users including an expert in hygiene and meets all 7 of Donald Norman’s principles for good user-centred design.
Through the development of the working principles prototype it was proven that the design would be technically possible to achieve. Several compromises were made in the prototype design to ensure that it could be completed within the project budget and time constraints such as moving to a single solenoid valve design and diluting the soap solution. Despite this, a fully functional prototype was produced that allowed cleanliness and user testing to be carried out. Again, the design received lots of positive feedback from users and the comments from Cheryl Herbert gave confidence to there being a market for this product.
However, the user testing also revealed some areas for improvement. The main flaw with the prototype was that it couldn’t produce soap foam very well, many users complained of it being too watered down. The earlier DS1 test prototype was much better at generating a foam. This also led to worse cleanliness test results compared to the earlier DS1 prototype. This problem is mostly to do with the fact that non-optimised off-the-shelf components were used. It is a solvable problem; it just needs further development. The main hurdle between reaching the detailed design stage of development and the current state of the project is gaining a better understanding of the foaming process since this is affecting both the cleanliness performance and the user experience of the product. This would be the focus of the next stage of the project if it were to be taken further.